Unlocking the Potential of Injection Molding Plastic in Metal Fabrication
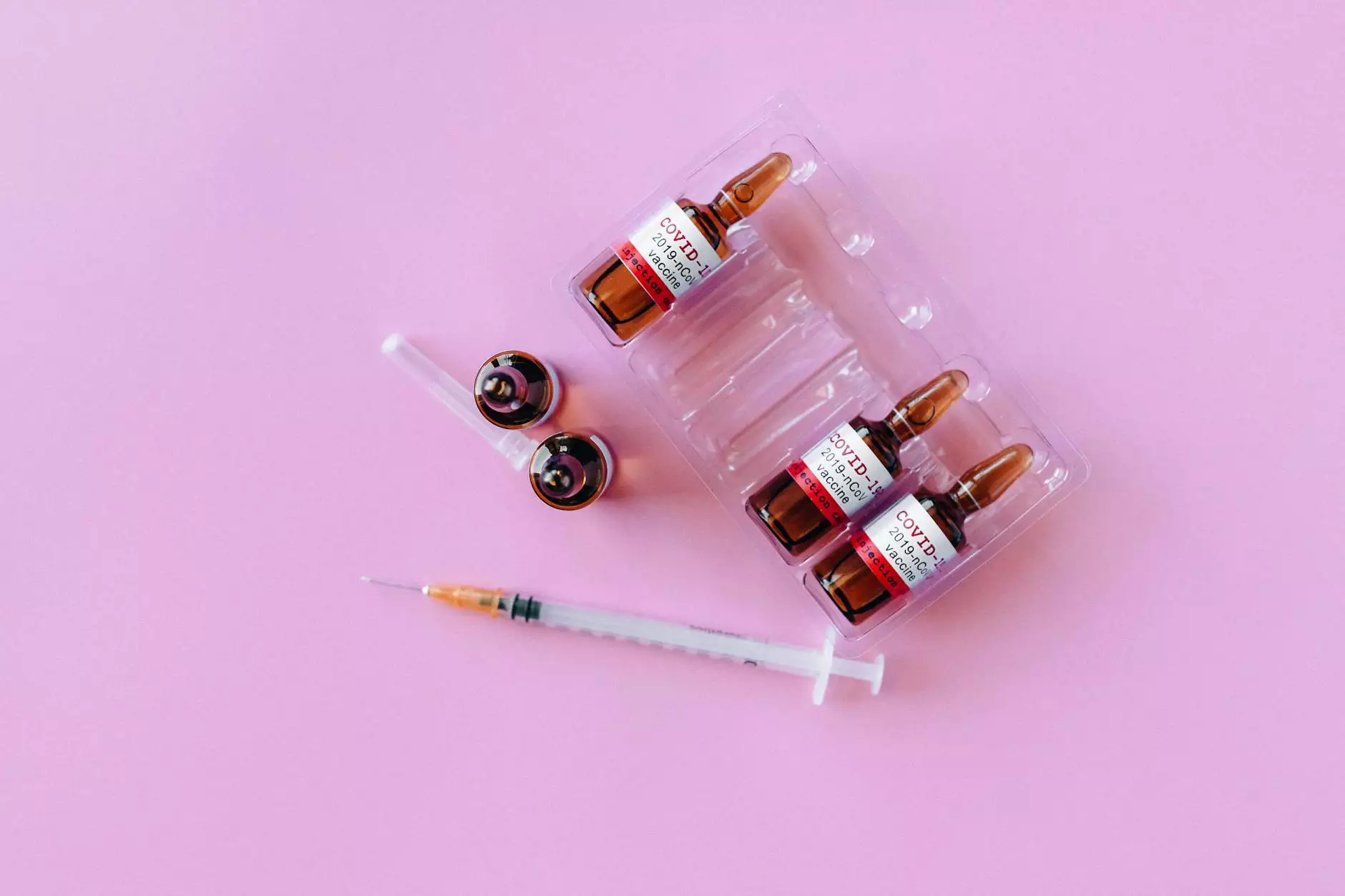
In today's competitive manufacturing landscape, the innovation behind injection molding plastic serves as a game changer, especially for industries reliant on metal fabrication. This article offers a comprehensive look at the impact of injection molding plastic in enhancing product design, optimizing production processes, and ultimately providing superior solutions to customers.
What is Injection Molding Plastic?
Injection molding plastic is a manufacturing process that's primarily utilized to create plastic parts. The technique involves injecting molten plastic materials into a mold, where it cools and solidifies, taking the shape of the mold. This sophisticated method allows for the production of complex shapes with high precision and efficiency, making it a cornerstone in the modern manufacturing arena.
Understanding the Injection Molding Process
To fully appreciate the value of injection molding plastic, it’s vital to understand its process. Here’s a detailed look:
- Material Selection: The first step involves selecting the appropriate thermoplastic material based on the required properties such as strength, flexibility, and temperature resistance.
- Heating: The chosen plastic pellets are then heated until they melt, becoming a viscous liquid.
- Mold Design: Custom molds are designed to precisely form the desired shape of the final product.
- Injection: The molten plastic is injected into the mold under high pressure.
- Cooling: Once injected, the material cools and solidifies, maintaining the shape of the mold.
- Ejection: After cooling, the molded part is ejected from the mold.
- Finishing: The final step often includes trimming and additional finishing processes to ensure quality and precision.
Benefits of Injection Molding Plastic
The advantages of using injection molding plastic are numerous, particularly for businesses in the metal fabrication field. Here are some of the most significant benefits:
- High Efficiency: The injection molding process can produce thousands of identical parts rapidly, enabling high-volume production.
- Complex Geometries: This process can create intricate designs that would be impossible or costly with traditional manufacturing techniques.
- Material Variety: A wide range of materials can be used, including various plastics, composites, and even metals.
- Reduced Waste: Injection molding produces minimal waste since exact quantities of materials are used.
- Reduced Labor Costs: Automation in the injection molding process minimizes the need for labor, significantly reducing operational costs.
- Consistent Quality: The controlled process leads to consistent, high-quality parts with minimal variation.
Injection Molding Plastic vs. Traditional Manufacturing Methods
When comparing injection molding plastic to traditional manufacturing methods, such as machining or casting, several key differences emerge. Understanding these can help metal fabricators make informed decisions about their manufacturing processes:
Precision and Consistency
Injection molding offers unparalleled precision and consistency in part production. Unlike machining, which can be prone to tool wear and variations, injection molding produces parts that maintain high tolerances with each cycle.
Cost-Effectiveness at Scale
While the initial investment for creating molds may be high, the cost-per-part decreases significantly as production scales up. Traditional methods often incur higher costs for labor and material waste.
Production Speed
Injection molding is much faster than traditional manufacturing, allowing for quicker turnaround times on projects. This speed is critical in today’s fast-paced market.
Applications of Injection Molding Plastic in Metal Fabrication
Metal fabricators are increasingly integrating injection molding plastic into their production processes. Here are some applications where this approach excels:
Automotive Components
The automotive industry relies heavily on injection molded plastic for parts like dashboards, bumpers, and interior components. The ability to create lightweight and durable parts enhances vehicle performance and fuel efficiency.
Consumer Electronics
In the consumer electronics field, the precision and complex designs achievable through injection molding have made it the preferred choice for producing items such as smartphone cases, computer casings, and components.
Medical Devices
Medical technology often demands high standards of cleanliness and reliability. Injection molded plastics are routinely used in manufacturing medical devices, offering the benefits of sterilization and biocompatibility.
Household Goods
Everyday items, from containers to cleaning products, frequently utilize components created through injection molding, providing convenience and durability in our daily lives.
The Future of Injection Molding Plastic
As technology advances, the future of injection molding plastic looks promising. Several trends indicate how this technique will evolve:
3D Printing and Injection Molding Integration
The convergence of 3D printing and injection molding will likely enable faster prototyping and design iterations, enhancing product development cycles.
Smart Manufacturing
With the rise of Industry 4.0, smart manufacturing technologies are being integrated into injection molding processes, leading to even greater efficiencies and automation.
Environmentally Friendly Practices
Sustainability is becoming increasingly vital. Advances in bioplastics and recycled materials for injection molding are paving the way for more eco-friendly manufacturing practices.
Conclusion: Harnessing Injection Molding Plastic for Business Success
In summary, injection molding plastic stands as a pivotal technology for metal fabricators aiming to enhance their offerings and operational efficiency. The benefits—ranging from streamlined production to unmatched precision—are undeniable. As industries continually seek innovation, injection molding will remain at the forefront, providing creative solutions to meet evolving demands.
By embracing this transformative manufacturing process, businesses can not only improve their product quality but also sustain competitive advantages in an ever-changing marketplace. The future is bright for those who harness the full potential of injection molding plastic in their operations.
For expert insights and tailored solutions in injection molding plastic, visit DeepMould.net, where cutting-edge methods and materials meet market needs.